Interfacing the thermal hydraulics advanced models with MELCOR severe accident codes
The CORYS advanced thermal hydraulics models are installed on most of the nuclear plant simulators in North America, as well as many in Europe.
It provides two-phase non-equilibrium models for the reactor coolant system, emergency core cooling systems, high energy systems of the balance of plant and containment/HVAC systems. The installation of the MELCOR severe accident models requires a complex integration of the thermal hydraulic “TH” models with MELCOR. When severe accident conditions are detected in the simulator, some of the TH models will be replaced on-the-fly with MELCOR. This requires that the MELCOR models be initialized to existing TH process values, and that interfaces perform this model transition smoothly.
MELCOR does not replace thermal hydraulic model of the reactor pressure vessel, but supplements it when a severe accident is predicted
A severe accident is presaged just prior to the start of runaway oxidation
At this demarcation, the training simulator thermal hydraulic models are use to determine the current conditions and creates a supplementary set of input that generates the base model and then starts MELCOR
After starting MELCOR, the thermal hydraulic model boundaries are used to interface with MELCOR and provide cooling or pressure relief
Obviously, a large amount of data will be required to pass between the two codes. The data interfaces are determined by the nodalization of the MELCOR models, which was carefully determined during the initial design of the TH/MELCOR product. Above is a diagram of the MELCOR nodalization for the primary system and a steam generator for a recent PWR project.
Several points are made with respect to the TH-MELCOR interface:
An interface is placed at penetrations to the Reactor Coolant System, e.g. steam line, feed water, injection lines, drain, relief lines
At each interface, thermal hydraulic models are used to control the injection or extraction rate of fluid (liquid or vapor)
Convective heat transfer between RCS and the containment atmosphere is modeled
Energy from the corium interaction with water and concrete is provided directly to THOR
Radionuclide information is used to provide feedback to the in-containment radiation detectors
MELCOR does not replace TH’s model of the reactor pressure vessel, but supplements it when a severe accident is predicted
A severe accident is presaged just prior to the start of runaway oxidation
At this demarcation, Thermal Hydraulic models determines the current conditions and creates a supplementary set of input that supplements the base model and then starts MELCOR
Extensive testing are then being performed with the TH/MELCOR solution to ensure that the integrity and accuracy of the MELCOR engineering code is being maintained while running in real-time. During our former project, many severe accident modeling experts came to the conclusion that the combined TH/MELCOR results are more accurate that the results obtained using the MELCOR models in a stand-alone configuration, as is done for engineering studies. This is due to the existence of high fidelity plant models that make up the MELCOR boundaries. Engineering runs are typically performed with static boundaries, which provide no feedback from systems connected to MELCOR. Below are results from the TH/MELCOR models versus the results of a MELCOR standalone models for a station blackout event.
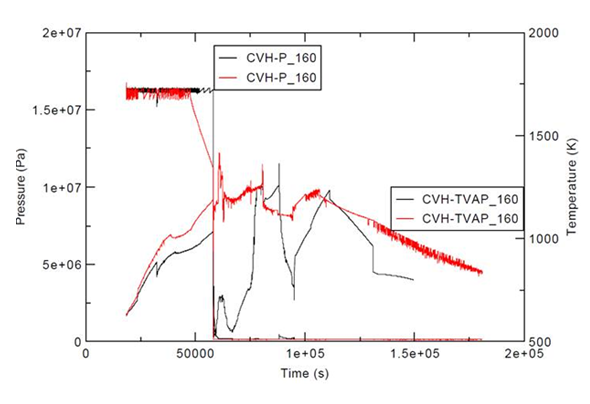
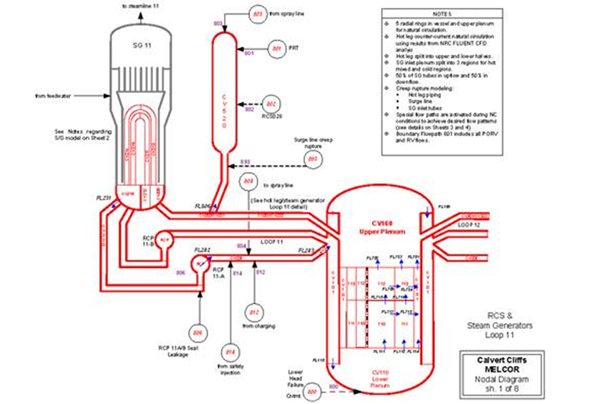