TRAINING
Simulators to improve
Nuclear Trainings
CORYS have been developing training simulators for the nuclear industry for many years from basic principle to replica full scope simulators
Full Scope Simulators
- Full Scale replica
- Digital Control Room
Full Scale replica
A proven training tool
Full scope simulator FSS allows training courses to be standardised, critical situations reproduced and verifies that procedures are applied correctly. The operation of actual installations is 100% accurate.
CORYS’ full scope simulators are quality full scale replicas of real equipment through real time simulation. Operators trained on our simulators acquire the skills necessary for effective nuclear power plant operation.
-
Key differentiators
- State of the art technology
- Knowledge of different types of reactors (EPR, VVER…)
- I & C experts
- Constant customer focus
Digital Control Room
Enhance your training capabilities
CORYS introduced the first and only ANSI/ANS3.5 compliant glass panel simulator in the industry. Perfect for a second simulator, the CORYS digital replica control room provides a low cost alternative to an expensive hard panel control room simulator.
The reduced version of glass panel simulator can easily be transported between classrooms and runs the same models as the full scope training simulator.
Whether your training requirements are overwhelming your existing simulator, or an easily configurable simulator is needed for engineering studies, a digital replica control room simulator provides a cost effective solution to your needs.
-
Full scale replica strengths
- Full-Scale Main Control Room replica, consistent with the real control room
- Fully tactile with haptic feedback, faithful to the operator actions
- Equipment handling design based on an explicit understanding of operators actions in the reference control room environment
- Equipment malfunctions available
- Robust, allows easy integration of real control room evolutions
-
Reduced replica strengths
- Mobile
- High-Resolution Touchscreens Interface
- Full-Size Annunciator Display
- Separate Navigation Touchscreen for Simulator Control
- Network-ready Instructor Station
- Ideal for Scenario Development and Testing
Basic Principles Simulator
Water pressurized reactor
Learning tools for Universities and Industry nuclear initial training
The integrated system developed by CORYS addresses the objective of reaching enhanced pedagogical objectives in the understanding of physical phenomena, plant process and cycle events of a PWR nuclear plant. These simulators provide a wide range of hands-on practical exercises to be combined with any kind of training content.
The CORYS training suite covers most of the needs of a nuclear training academy or university offering nuclear engineering degrees. These tools can also be used to train any person working in the nuclear industry in order to improve general knowledge of nuclear power plant design and operations.
CORYS training suite comprises 3 off-the-shelf set of simulation tools which enhance training people from power plant normal operations through severe accidents and up to I&C regulation design.
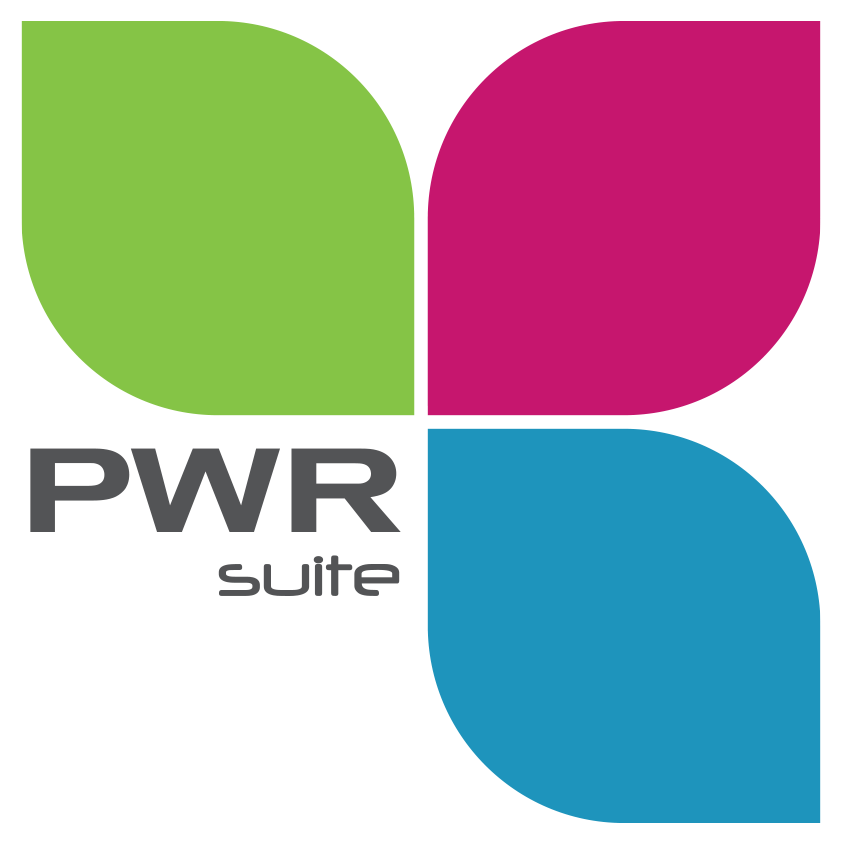
- Normal operation
- Accidental operations
- Micro-simulation modules
C-PWR
Dedicated to PWR physics principles and normal operations
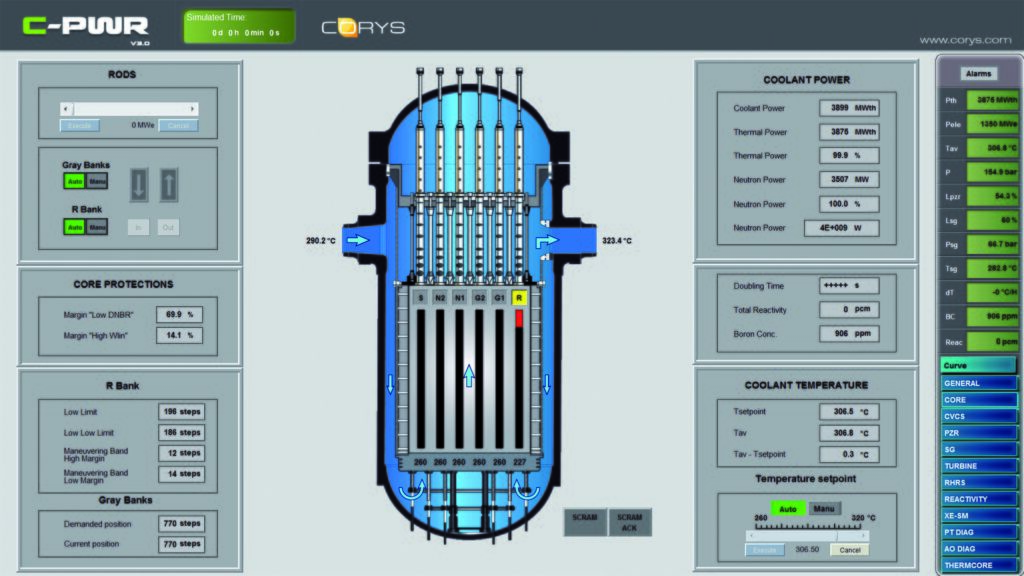
Understand and master all PWR principles and concepts!
C-PWR is operated without following procedures. Discover all the main steps of a PWR cycle (shutdown states, criticality, synchronization to the grid, stretch-out operation). I&C safety system has been simplified to allow a try and improve approach on basic operations.
Basic principles from cold shutdown to stretch out operations
-
Training objectives
-
-
-
X-PWR
Focus on abnormal procedures and accident handling training
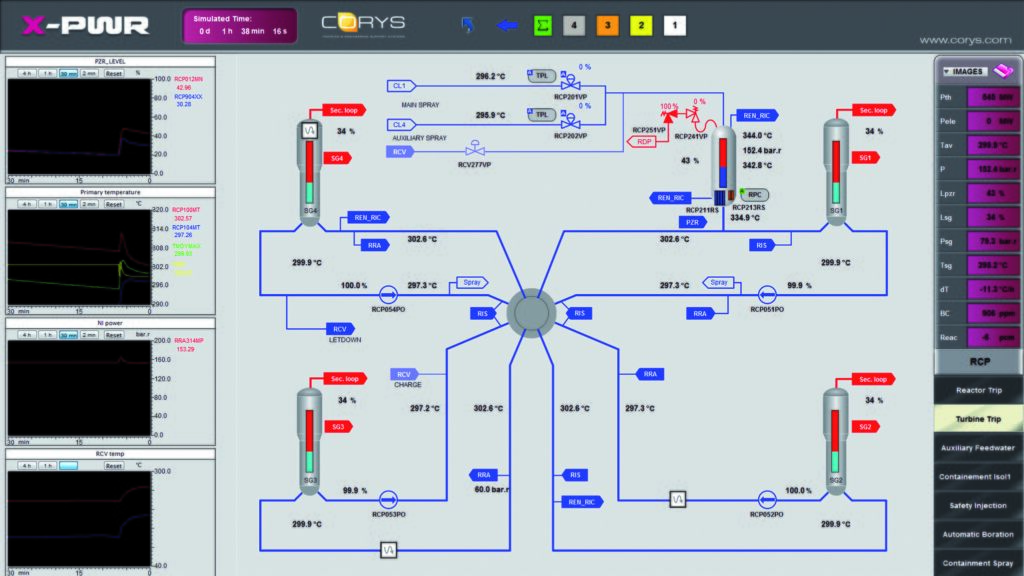
Larger scope, dedicated to accident management training
X-PWR is a more advanced simulator that requires the use of operating procedures. It is designed to go through main accidental situations and to discover the plant auxiliaries. Its I&C structure is close to an actual one.
A dedicated I&C HMI enables understanding all principles and studying I&C tuning impact on systems behaviour.
Accidental situations and I&C detailed design
-
Training objectives
-
-
-
M-PWR
Training modules about specific systems and control channels.
M-PWR is a set of modules that provides dedicated self-training on systems or control channels of a large number of PWR reactors. Modules cover 1300 MW, 900 MW and EPR reactors.
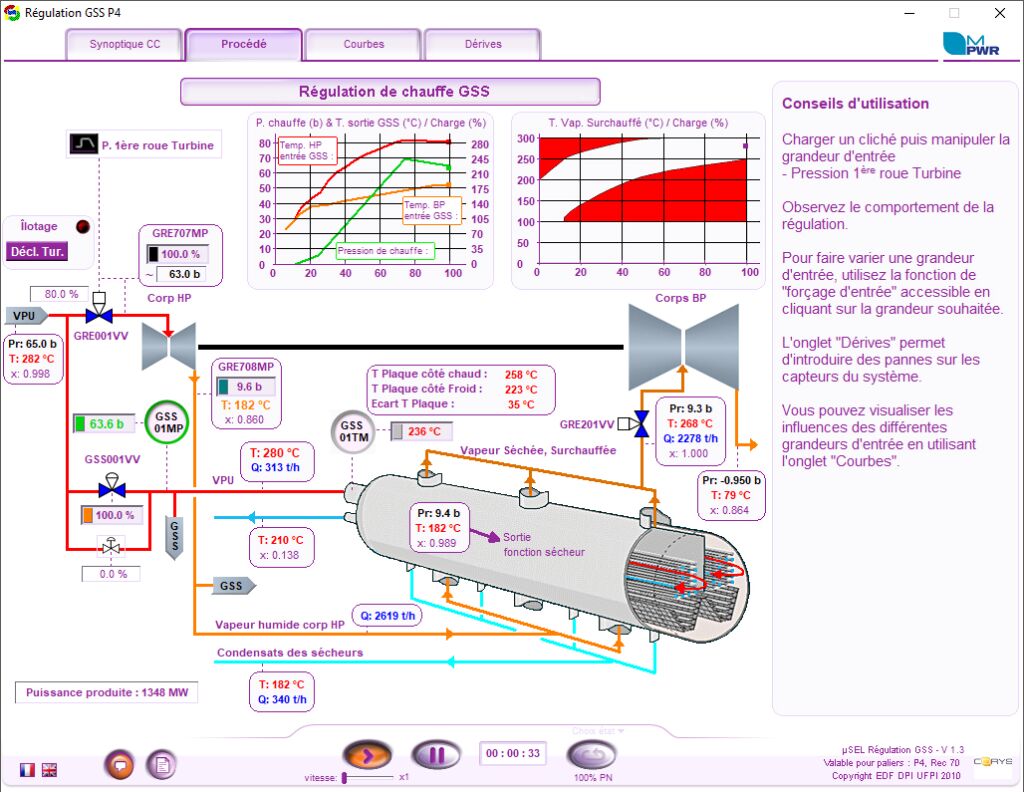
For classroom trainings and e-learning (on-line access)
Self-learning approach on standalone systems / I&C / equipment
Specific training
- Internal & external flood model
- Severe accident
- Refuelling machine simulator
Internal & external flood model
A first engineering principles flooding model for nuclear power plants
High fidelity models create realistic flooding conditions for both internal and external flooding events.
Plant terrain, buildings and equipment, and external sources of flooding are replicated so that the simulator response duplicates the actual plant.
Flooding of facilities, equipment and electrical distribution results in accurate failure response for training operators and managers on high probability/high risk flooding events.
Turn a classroom procedure review exercise into a realistic simulator scenario for maximum training value.
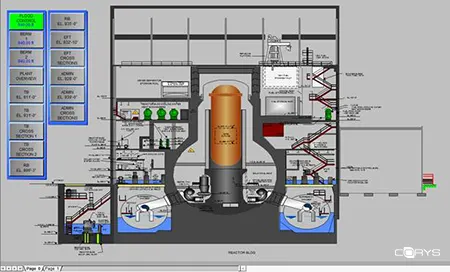
Internal flooding
-
Strenghts
- Replaces paper procedures
- Real elevation accurate
- Dynamic images of flooding events
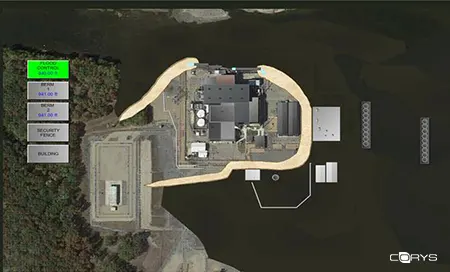
External flooding – Mississippi River Flooding Scenario at Monticello Nuclear Station
Severe accident models
The MELCOR severe accident models allow core damage scenarios on training simulators
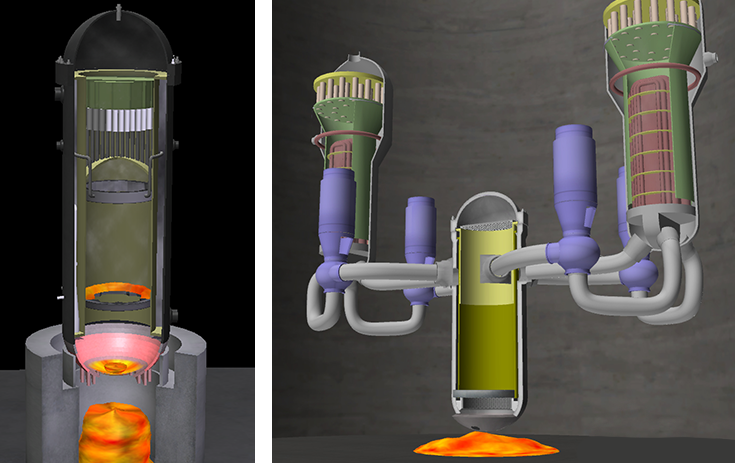
In the aftermath of the Fukushima disaster nuclear stations recognized the inadequacy of operator training for severe accident response.
Severe accident mitigation guidelines had historically been covered by classroom exercises and procedure reviews. CORYS now provides high fidelity simulation of core damage scenarios on the plant training simulators.
The simulation accurately reproduces core heatup, core displacement, loss of cooling geometry, core meltdown, reactor vessel breach, and molten corium displacement onto the containment floor.
Containment environment response is modeled, allowing operators access to containment parameters necessary to diagnose reactor core and vessel conditions.
The severe accident models are critical for operator training, accident procedure validation and emergency response drills. Includes detailed 3-D dynamic graphics to help facilitate understanding of accident progression.
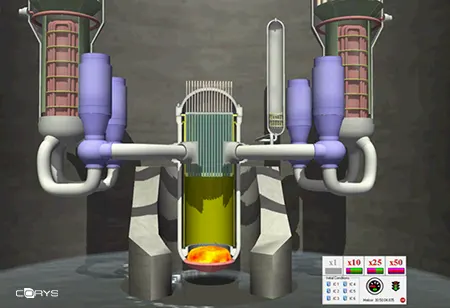
Refuelling machine simulator
Fuel loading and unloading
CORYS has developed a fuel loading/unloading simulator to train fuel handling teams. The simulator enables very complex operations to be carried out to unload all the fuel first and reload it entirely between the Reactor building and the Fuel building.
This simulator includes a whole host of innovations: connection to PLCs, 3D images, a mobile version, and more.
-
Fuel Loading simulator strenghts
- Refresh knowledge on rarely practiced operations
- A realistic virtual environment
- Combination of the virtual world and actual Programmable Logic Controllers
- Coordinating movements with millimetre precision – 15 metres underwater
- Simulate the identification of fuel rod assemblies
- Four employees will be working at the same time