PROCESS SIMULATION
A Worldwide Leader
in Simulation
CORYS is a global leader in real time high-fidelity dynamic process simulation, engineering, and training for process industries.
Our products and services provide world-class experiences that set new standards in operator training by teaching energy efficiency, reliability and safety.
Headquartered in Grenoble, France, we have delivered simulators in more than 60 countries.
We support a worldwide fleet of more than 2600 simulators.
Industries
CORYS serves all process industries, ranging from upstream offshore platforms to downstream refining, chemicals, and polymers. We also support new biofuels technology, as well as renewable energies, and midstream companies.
Solutions
CORYS’ core solution is dynamic process simulation that accurately simulates your process across a wide range of conditions including start up, shut down, and steady state operations. We also provide engineering and training solutions to support the use of simulation in your organization.
Products
With products ranging from our Companion Training Manual to 3D immersive simulation, we have the ability to meet our customers’ training and simulation needs and help them ensure safe and efficient operations.
An Global Footprint
dynamic models delivered to Process industries
countries
The CORYS Advantage
Lower TCO
High fidelity simulators recognized by the industry and flexible solutions designed to last
On-time delivery
Our OTD rate is 99% and we are experienced in building during rolling stock production
Responsive service
Local project managers and support experts onsite worldwide
Partnership
Committed to ensuring customer satisfaction and meeting our customer’s needs
Innovation
Commitment to investment in research to ensure we are delivering the latest in simulation technology
Community
What our customers are saying
- INDISS PLUS is using one single light simulation server easily while other requires heavy servers for the same scope.
- INDISS PLUS is very robust and server has not face speed problem issues after installation at site.
- INDISS PLUS includes an efficient and very user friendly instructor platform with Automatic Training Exercise and Trainee Performance Monitoring.
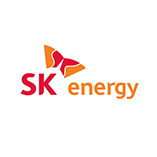
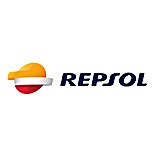
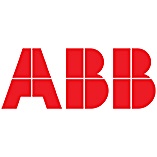
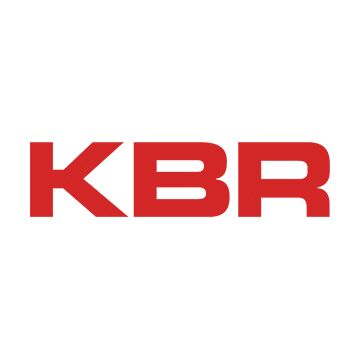
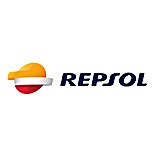
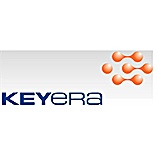
Process Industries News Updates
Petrobras Elevates Refinery Training with Innovative Digital Simulation from CORYS
Petrobras has taken a bold step in digital transformation by selecting CORYS to deliver an advanced Operator Training Simulator (OTS)...
Petrobras Elevates Refinery Training with Innovative Digital Simulation from CORYS
Petrobras has taken a bold step in digital transformation by selecting CORYS to deliver an advanced Operator Training Simulator (OTS)...
Unlocking ROI and Value: The Power of CORYS + Dsider
In today’s fast-evolving industrial landscape, smarter decision-making is critical. The partnership between CORYS and Dsider combines dynamic process simulation with...
CORYS joins the Symbio Hydrogen Academy: a new dimension in hydrogen training
CORYS joins the Symbio Hydrogen Academy consortium as its ninth member, marking a new stage in the development of hydrogen...